Tests
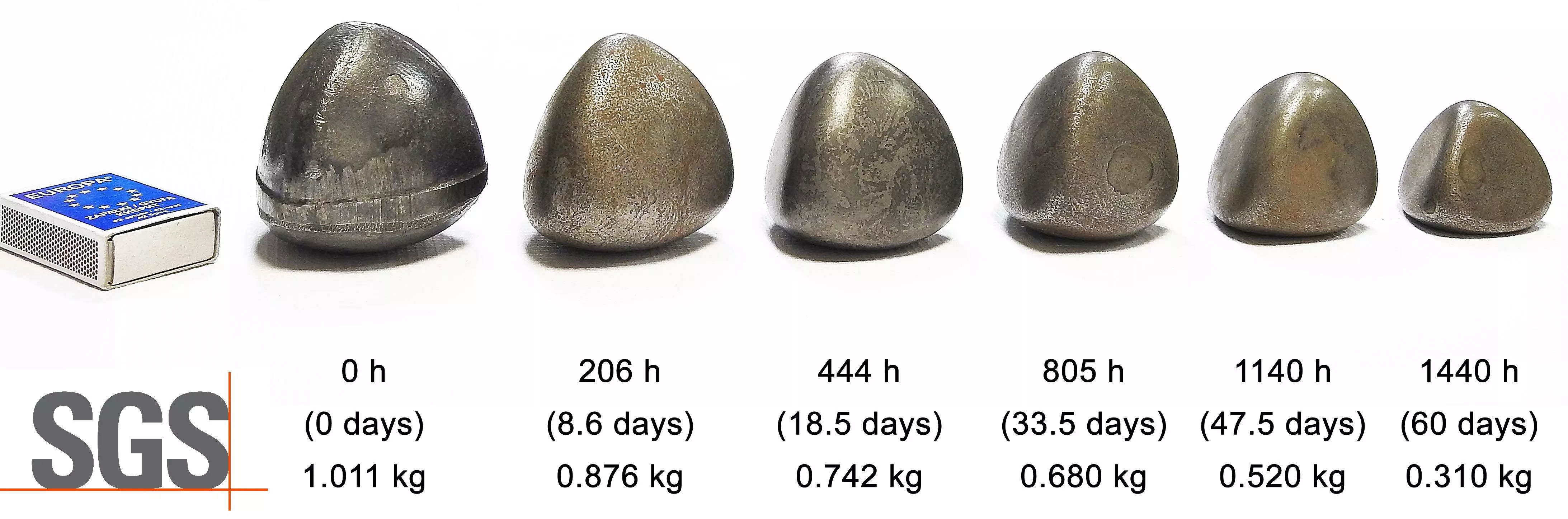
In 2019, we have successfully added several new tests to the laboratory and industrial tests of RELO grinding bodies, conducted so far:
• The international laboratories of the prestigious mining consultant and our technical partner Wardell Armstrong International (https://www.wardell-armstrong.com) conducted laboratory tests of RELO grinding bodies in June 2019. The tests have once again shown the excellent results of RELO and have reaffirmed RELO’s superiority.
• Immediately afterwards, the German-Mongolian Institute for Resources and Technology (GMIT) (http://www.gmit.edu.mn) conducted two-week laboratory tests performed by a German-Mongolian team of distinguished specialists. Our partners from the institute have achieved yet another scientific success for RELO. The results showed once again that RELO is the better solution for grinding bodies.
With the new tests we already have results from 6 independent laboratories and mines in Europe and Asia, which all show that RELO is the future of grinding bodies!
Download the reports from the tests in 2019
![]() |
![]() |
Lab test by Wardell Armstrong International Laboratories - June 2019 | Lab test by German-Mongolian Institute for Resources and Technology (GMIT) – July 2019 |
The new reports supplemented the laboratory and industrial tests performed so far. As a continuation of the successful laboratory test conducted at the Erdenet Mine in 2017, the new tests have given us the confidence to continue with a big industrial test again at the Erdenet Mine, which is forthcoming.
Download the report from the tests in Erdenet in 2017
![]() |
Lab test with Bond mill by Еrdenet Mine Laboratory - November 2017 |
The inventors tell about the laboratory and industrial tests of RELO grinding bodies conducted throughout the years:
“In the process of research over the years we have created a number of different models for the different needs and applications - for dry or wet grinding, for harder or softer materials, and with them we performed certified by SGS tests in the famous for this purpose Bond mill. Our first surprise was when we analyzed the results and found out that in all cases, the Bond index was lower than all other high quality bodies listed in the catalog of Bond himself. In other words, we talk about that the experiment with the different grinding bodies showed more efficient, much less energy- and time-consuming, more compact and in the same time – with higher productivity.
These results gave us the confidence to perform the expensive industrial tests - in an environment as close as possible to that of those who use grinding bodies, and these are thousands of businesses, companies, dozens of industries using mills, either for dry or wet grinding of ore, cement, gypsum, lime, feed, paint and chemicals, recycling and whatnot.
After some research we found a mine, that only three months ago had completed a European project for building a completely new installation with two not very big 8-ton mills purchased from China which grind with 60 mm grinding bodies, very hard ore which is with 65% quartzite and up to 7% lead. “
Engineer Vassil Gentchev – Inventor
“Together with SGS we conducted industrial tests of our bodies, along with analogous to them 60 mm spheres. We put in two identical industrial grinding mills standard grinding bodies and RELO bodies, Model M-1.1
We conducted approximately 6 months of preparation and industrial tests in a real environment. For this purpose, we produced the required amount of tetrahedron bodies in one of the mills and began testing.
The tests lasted about two months, during which we constantly compared the results in the two mills … “
Engineer Petar Bodurov - Inventor
During a prolonged milling in real conditions it proved that the bodies retain their shape and thus their efficiency.
“Three months of extensive research showed that the model M1.1 is with over 97% higher performance under exactly the same conditions with the spherical bodies. And the cost of electricity fell by over 43% per ton. In this case, no other explanation exists, except that a radical change in the grinding process in the mill is happening, and this is due to the specific advantages of the new form.”
Engineer Petar Bodurov - Inventor
“Having the same material, sizes, and under the same conditions in exactly the same environment, our surprise was great - I must tell you that these are extraordinary high results both in saving time and energy, and in production. Productivity increases and energy costs fall, the lifespan of the bodies also rose threefold, so to conclude - outstanding results and differences with the current grinding bodies. And this - with the most severe for grinding materials.”
Engineer Vassil Gentchev – Inventor
During the conducted industrial tests, aside from the two times greater productivity, which drastically decreases costs, it is also observed an improved quality of grinding, which helps to increase the utilization of the valuable particles during the flotation. The results of the sieve analysis of the conducted industrial tests with lead-zinc ore demonstrated the presence of 9.63% more lead particles below 75 microns, which causes direct improvement in the extraction of valuable particles during the flotation treatment of the ore.
RELO work in the mill - 3D Simulation
How RELO Grinding Bodies work in the mill - 3D Computer simulation
The new computer simulation with the RELO Grinding Bodies demonstrates in detail the process of working in the operating mill. This is a really good method in which, using modern computer technologies, we can visually see what happens inside the mill. With the help of this technology, we created 3D models of the grinding bodies which are placed in an environment where they are dependent on the laws of physics for matter and gravity. Thus, they simulate with great precision work in a real environment. Thus, we can see that during operation, the material, the water and the grinding bodies are mixed together, and gradually, at one end, in the direction of rotation of the mill’s drum, the grinding bodies begin to climb the wall while adhering by the centrifugal force and the wavy relief of the drum lining. The lower center of gravity of the RELO bodies and their more rounded sides allow them to start climbing the wall of the drum more easily and to go higher than the spheres, thus placing themselves on the lining with their rounded side, and not with their edges. Upon reaching the upper point, the bodies begin to fall downward in the direction of the material, which also leads to greater kinetic energy during the falling on the material. Thus, the fragmentation of the material becomes much faster and more efficient. During the industrial tests which took over 60 days (1440 hours) and during the observed simulations, we have ascertained that the way in which the RELO Grinding Bodies behave not only does not damage the lining of the mill, but even demonstrates minimized wear. Whereas, at the same time, the spherical bodies (due to their smallest surface and their spherical shape) have the smallest contact spot, which in combination with their round shape, makes the climbing in the mill slower and more difficult. Thus, the sphere spins mainly around its own axis, and it takes time for it to start climbing. This rotation, however, resembles sandpaper, which gradually removes layers of metal from the lining during work by scouring the mill lining and leads to its greater wear. These factors and the lack of effective grinding elements, such as 120 degree edges and a larger contact surface, significantly reduce the effective crushing and grinding of the material and ruin the lining more quickly. In this way, the tests and practice show that the sphere turns out to be the most inappropriate form of grinding body.
Download reports and certificates of industrial tests
![]() |
![]() |
SGS certificate report - RELO Industrial tests 2017 EN | SGS certificate report - RELO Industrial tests 2017 BG |